How to Survive the Crisis in Lumber Prices
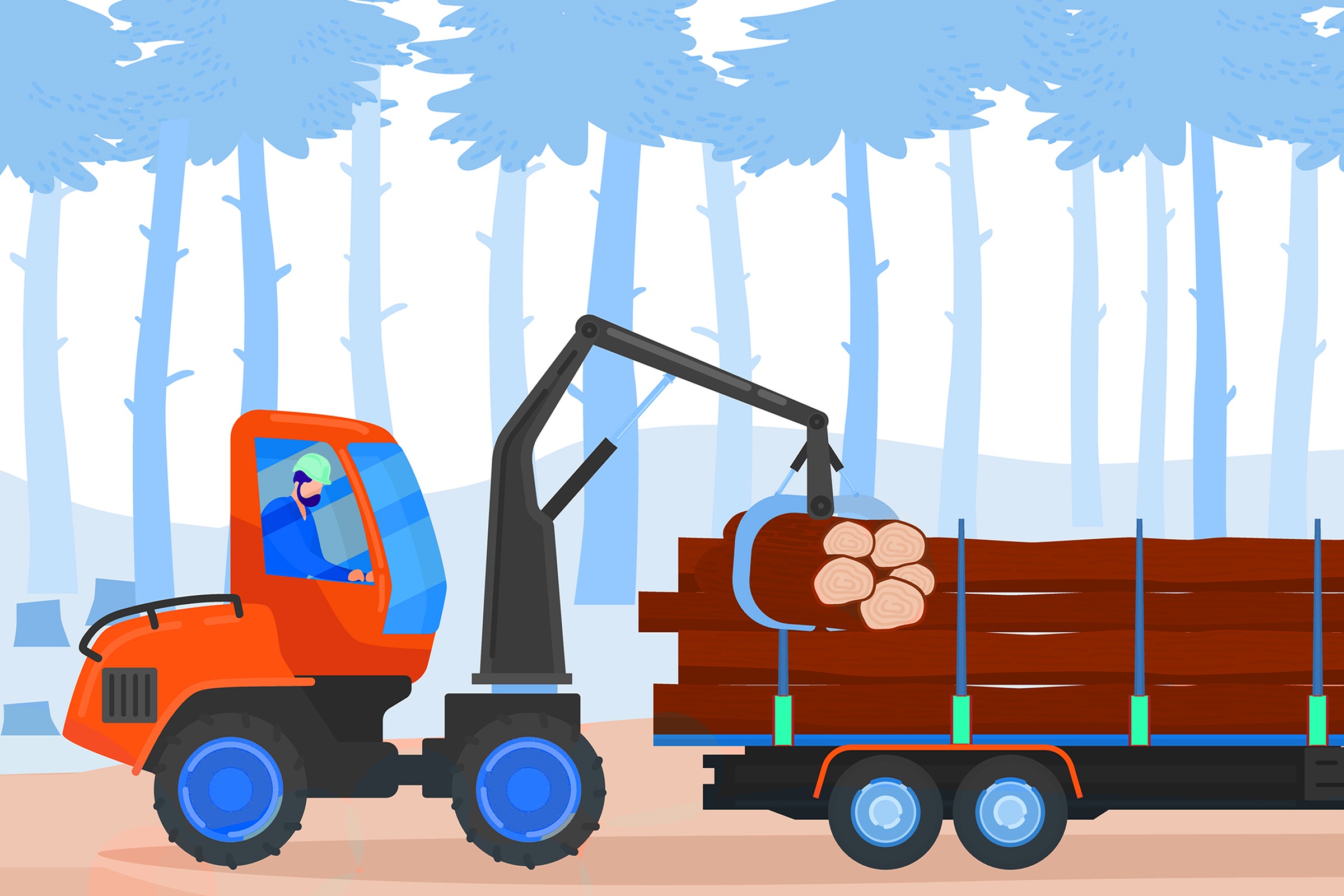
3 Practical Strategies for Managing Lumber Price Volatility
Unless you’ve been asleep for the last year, you’re probably aware that a spike in lumber prices is one of the biggest problems facing the construction industry today. Indeed, it would’ve been almost impossible to escape dire warnings of “skyrocketing prices” and “record highs” plastering popular construction news sites or the panic over the crisis being pushed on social media.
While the industry has been eager to push panic over sky-high prices, it still hasn’t shed light on what caused the problem or provided a real solution to it. Recently, we showed how prices across the industry have surged due to COVID-19 and also provided ways to lower costs by eliminating waste, but lumber price volatility is a unique problem that requires a unique solution.
What’s Causing the Skyrocketing Lumber Prices?
So what caused the problem? Initially, surging demand at the start of COVID pandemic pushed housing inventories to record lows. Although contractors got back to work and started building homes, the lumber industry has been playing catchup ever since. When initially confronted with the news of millions of unemployed at beginning of the pandemic, mills shut down production and stymied the lumber supply chain. According to Robert Dietz, the chief economist at NAHB, the tightening of the supply chain is negatively impacting the cost and availability of lumber and other materials, increasing demand.
As a result, prices are now up 250-300% from where they were last year before the pandemic hit:
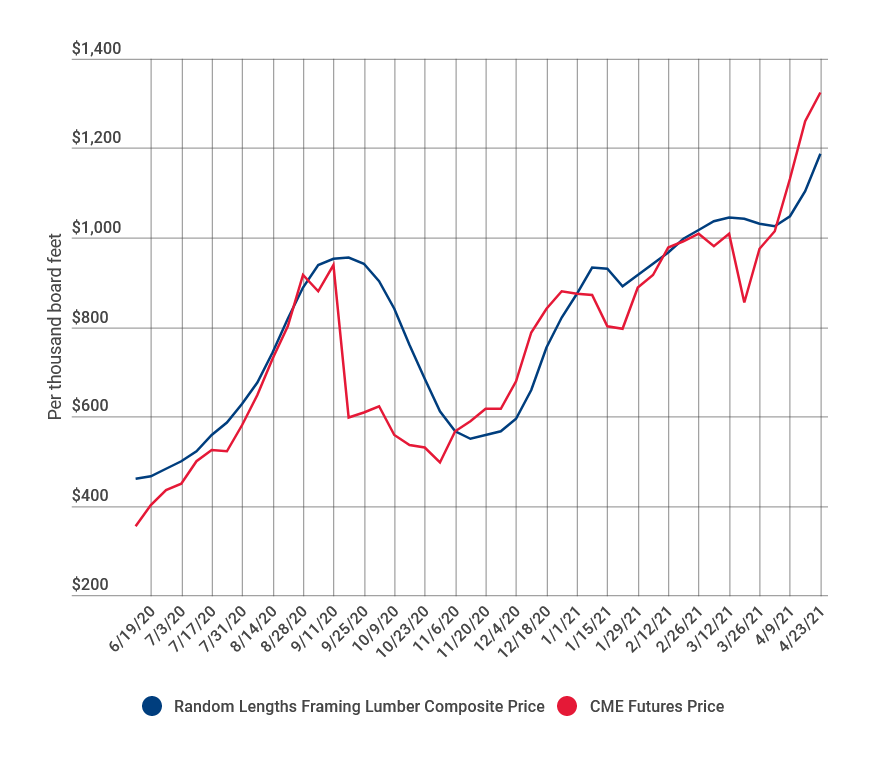
Source: NAHB
In fact, soaring lumber prices have increased new single-family home prices by $36,000 and almost $13,00 for multi-family homes since April 2020.
But the increase in demand is deceptive--skyrocketing lumber prices are actually threatening the housing boom. Median home prices, which have jumped to a record-breaking 17.2%--levels not seen since the height of the housing bubble in 2006--could dampen demand for new homes and are already wreaking havoc on residential builders. If you need a cost estimate for a residential home project, check out our comprehensive guide on how to develop the most detailed and accurate cost estimate for a new home.
While many experts expect prices to come back down by 2022, the supply chain is likely to remain stalled given the U.S. still has to complete trade negotiations with Canada, which supplies the U.S. with roughly 30% of its lumber. Such headwinds are never great news for builders, but particularly residential builders, who are struggling to get more jobs as soaring prices reduce new home construction demand. Indeed, the price volatility producing sharp increases in lumber prices is now being called a genuine “crisis.”
How Can We Solve the Lumber Price Crisis?
So what can you do about this lumber crisis if you’re a builder? Here we provide three practical strategies for contractors to employ to help you better navigate lumber price volatility in the coming months:
Strategy 1: Use Alternative Materials
According to a poll conducted by Construction Magazine Network in 2020, at least 75% of contractors are interested in or pursuing alternative materials to lumber:
- Metal Framing: Metal framing is one of the best alternatives to traditional lumber framing. One advantage to using metal framing is that builders no longer have to wait in line for their wood shipment and can buy their own machines to make their own materials.
- Tension Fabric: Tension fabric buildings are a great alternative to wood, especially for those in agriculture. In fact, the traditional skill-set of wood builders and/or carpenters is all you need to work with and create tension fabric buildings.
- Engineered Wood: While traditional solid sawn lumber remains popular with residential builders, as lumber prices soar, many builders are looking into the benefits of engineered wood. Not only is engineered wood cheaper than typical lumber prices, but it can also provide more size flexibility. Some of the most in-demand products include prefabricated wood I-joists, glue-laminated timber or (glulam), and laminated veneer lumber (LVL).

Strategy 2: Add an Escalation Clause to Your Contracts
If using alternative materials is not an option, NAHB recommends preempting the problem of lumber price volatility with an escalation clause, which allows a contractor to charge the project owner for an unexpected but “predetermined material cost percentage increase.” In short, escalation clauses simply ensure that in the event building materials and lumber prices increase, the customer will be responsible for paying the difference. Escalation clauses are a great risk management tool for contractors and also help to notify customers in advance that contracts could change in the future due to supply issues that are outside the builder’s control--improving communication and increasing trust between parties.
If you’re not sure how to draft an escalation clause for your next building contract, we’ve taken the liberty of providing a few examples.
Strategy 3: Use A Cost Estimating Service to Get Real-Time Prices
By using cost estimating service, contractors can easily sidestep the risk of soaring lumber prices by relying on a professional who can help them navigate changes in the market. 1build’s cost estimating service connects with suppliers across the country to get live, local material rates in your zip code. In short, 1build’s cost estimating service is the best way that builders can submit the most competitive estimates without sacrificing their bottom line.
Worried about skyrocketing lumber prices? Want to get the best possible prices so you can win more bids while maintaining your margins? Sign up today to learn more.
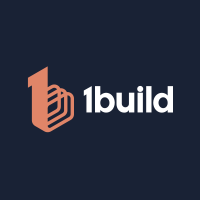
1build provides an easy-to-use integration with construction supplier catalogs and purchasing systems. Get access to millions of construction materials with our API today