Estimating a Framing Takeoff Cheat Sheet
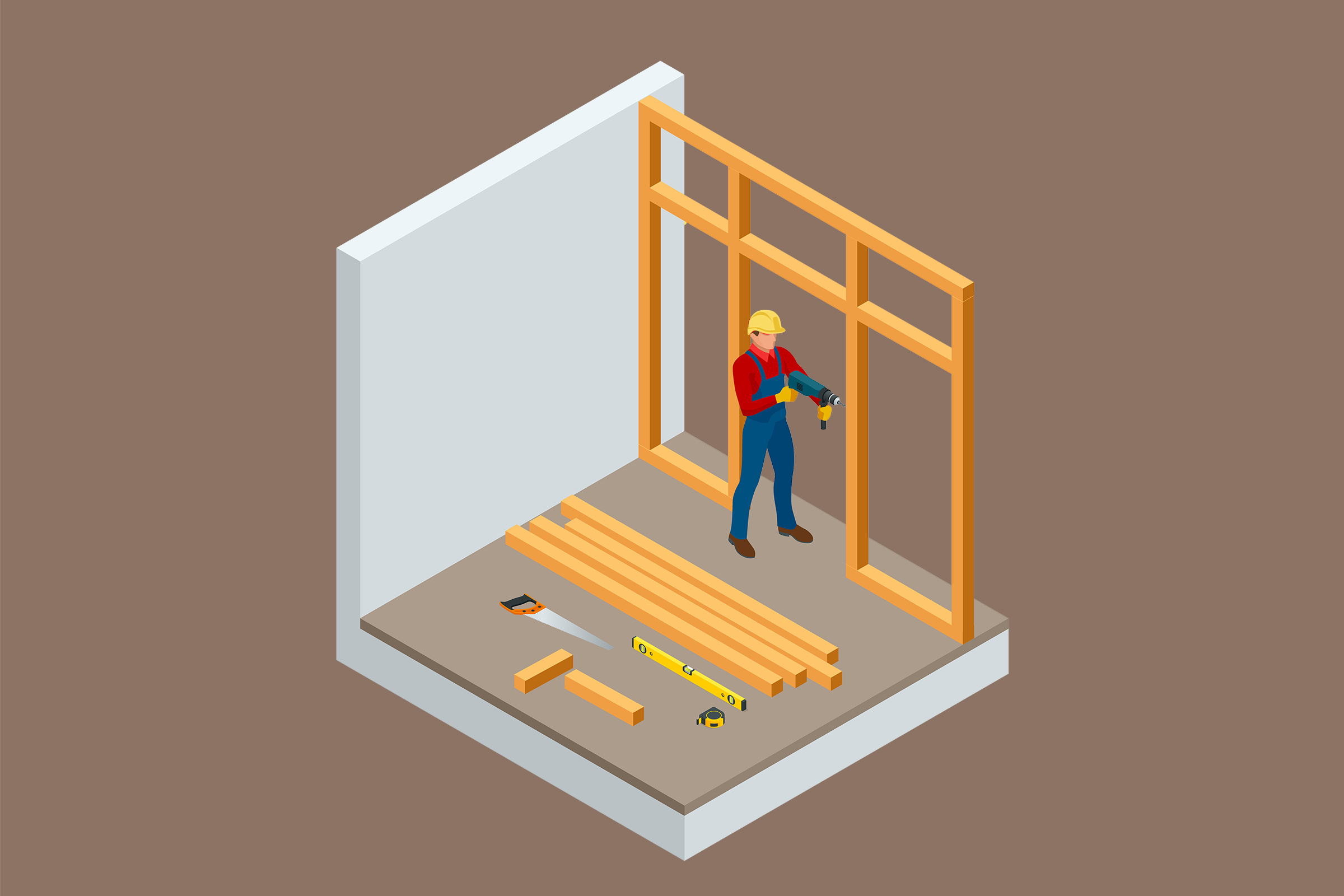
The Quickest Way to Get Your Next Takeoff Done Accurately
With global construction costs expected to rise by 4.3% and accounting for about 7% of the U.S. gross domestic product, is it any wonder that being able to properly calculate a framing takeoff can help to determine how successful your construction company will be? But with a mean annual wage of $71,350, hiring an experienced, knowledgeable cost estimator may be an additional expense your company can't afford. That being said, estimating a project's costs accurately can be almost as difficult as trying to estimate the timetable needed to get the job done. Fortunately, we've put together this guide to help you create an accurate framing takeoff estimate for your next project, including some tips and tricks to make the entire process, from initial estimate to final punch list, easier than ever.
How to Estimate a Framing Takeoff
As part of the materials side of your estimate, a framing takeoff allows you to determine exactly how much of what type of lumber you need to frame out a structure. It's not the entire process, because you'll still need to figure out any other materials you'll need as well as how much your labor costs will run, but it can be a big part of your project expenses, so it's important to do it right. If your calculations are off or if you're wasting too much material because you haven't taken advantage of longer boards or similar efficiencies, you could end up losing a lot of your profit, making it harder to see your company through the next big project.
Similar to other types of takeoff, a framing takeoff looks at exactly how much of which materials you'll need to be able to complete the project. It’s often limited to materials of a specific quality, appearance, manufacturer, engineered strength, or similar specific performance benchmarks to ensure all bids will meet specific quality control minimums. In framing, this may involve framing members of a specific dimension, using engineered lumber for floor joists, plywood rather than OSB for sheathing or subflooring, nails or screws of a specific length or meeting specific standards for fasteners, adding stucco wrap instead of standard house wrap or pre-built trusses for the roof.
It's easy to get caught up in wondering exactly what you should and should not include in your takeoff. Does it include safety equipment, such as fall-prevention tools and safety glasses? What about the sports drinks you provide to your crew during the high summer months to prevent dehydration and heat-related injuries? Generally speaking, you'll only count the materials that are going into the project itself in the takeoff, not the additional materials that, though you wouldn't use them if you didn't have the job, are not a part of the overall structure. Materials, tools, and supplies such as these would be counted in the labor side of the equation, as would rental equipment that you need to retain to get the job done, but will not remain a part of the structure once it's completed.

This process can include components or raw materials, such as sand, cement, and aggregate used to pour the piers for a backyard shed, as well as pre-assembled components such as using concrete deck blocks in place of cast-in-place piers. There are four types of material measurements to take into account when you're creating a framing takeoff for an upcoming project. These include:
- Count: As an example, if you're building the shed that we'll discuss in the next section below, how many nails, screws or other fasteners will you need to get the job done? It's often fairly easy to develop a "cheat sheet" to use with this if you're doing manual takeoffs, such as knowing how many nails it will take to secure the ends of a stud to a top and bottom plate, how many fasteners are used to create a window or door opening and how many fasteners it will take to fasten a sheet of sheeting or subflooring to the framing members, so all you would have to do is count the number of connections of a specific type--for example, the number of studs, the number of sheets of sheeting or the number of windows. Then you would take that count of connections and multiply it by the number of fasteners it uses to determine how many overall fasteners of a specific type you'll need to get the job done. You could also look at the number of hinges per door or similar aspects of other types of construction beyond your framing takeoff.
- Length: How many eight-foot studs will you need? How many ten-foot floor joists? Are there areas where you can get multiple framing members from a single board? For example, if your structure has two three-foot wide windows, you know that you'll need two 2x4 boards over the top of each window. You could cut them from a pair of eight-foot boards or from a single fourteen-foot board while minimizing waste. Start by counting the length and size of your top and bottom plates, then your studs, remembering to double up where needed around windows, doors and corners. Once you've finished with those, go back and see how many headers you'll need of what length to go over the top of each opening, as well as whether you'll need prop boards, fire blocking, or similar additional lumber to meet codes or work safely. In addition to a framing takeoff, you'll often see length referenced for electrical wire, plumbing, gas lines, and similar measures of materials at length.
- Area: When you're looking at general construction, area measurements help determine how much flooring, paint, or drywall panels will be needed to complete a project, but in framing, this most often refers to roof decking, wall sheathing, and subfloor. Unless you're using balloon framing techniques, the subfloor will extend to the edges of the floor, rather than the inside of the walls, as you'll be building a platform and then constructing your walls on top of that platform. As the walls are going up, they'll need sheathing added to keep the elements out, while the roof will require decking in most situations to support the roofing materials, especially when using shingles, rolled roofing, and tiles that require being fastened down very frequently. Make sure to check what thicknesses are needed, as walls will often require thinner material than subflooring or even roofing may demand, providing you with an option to save money on the project materials cost.
- Volume: Generally used in earthworks, site preparation, and foundation work, volume is a measure of how much of a material is needed to fill a specific area, such as gravel for backfilling a slope, concrete in a foundation or similar measurements. Though you don't see as much of them in a framing takeoff, you may occasionally, especially on small projects, be asked to also provide piers or footers as a foundation in addition to your framing work. For that reason, it's important that you're able to calculate these measurements and determine what volume will be needed. This can include backfilling the bottom of a trench or pier with gravel or sand for drainage, casting a pier or footer in place made of concrete, or similar details. Knowing how much volume is needed makes it easier to determine whether it is more cost-effective to mix the materials on-site yourself or to hire in a ready-mix truck to bring the materials to you. Volume is calculated by multiplying the measurements in feet of length, width, and height to determine cubic feet. To determine cubic yards, divide by the 27 cubic feet that are in a single cubic yard.
Easy Tricks to Maximizing Your Framing Takeoff
However, simply counting the material isn't necessarily going to give you the best possible material usage. Let's start with a basic structure as an example. You have a client who needs a storage shed built in their backyard, with a six-foot by eight-foot floor, a rear wall at seven feet tall, a front wall at eight feet tall and up to a one-foot overhang on either end. You could cut the entire frame from 8' 2x4 and 2x6 lumber, but that's going to leave a lot of scrap material. How can you optimize your cut list to reduce how much waste you have?
If you purchase twelve-foot 2x6 lumber for your flooring joists, you can cut them in half for your floor joists instead of having to buy two eight-foot 2x6 studs and then having to cut two feet off as waste material. For your seven-foot rear wall, instead of cutting a foot off of an eight-foot stud, you'll be able to get two seven-foot studs out of a fourteen-foot board. Your front wall and rafters can be from common eight-foot stock. This approach drastically reduces the amount of waste you need to get off the job site when you're done.
However, there is another concern. If you purchase your materials based on these assumptions, but fail to communicate your cut list to your framing crew, there's a good chance they'll simply cut down the eight-foot 2x4 boards for the rear wall, the eight-foot 2x6 boards for the floor joists and then sit there scratching their heads to try to figure out what to do with the extra twelve-foot and fourteen-foot boards. If you decide to take this approach, you'll need to figure out a way to communicate this information to your framing crew.
One option is to create a cut list as you develop the framing takeoff. As you work through the blueprints, you can start by tracking how many of each length you'll need, as simple as keeping hash marks for each measurement. Once you've assembled the entire list, you can go back and determine how many longer boards you may need to optimize your cut list. From there, you can create a master cut list, showing which boards are being cut to what length, across your entire project's material list. Another advantage this approach has is that when you're facing bad weather and have a crew that wants to work, they can work through the cut list in your warehouse or shop, getting all of the materials--and possibly even some pre-assembly--ready to go, so that you can take advantage of better weather without losing productivity.
When you take the time to understand how to create a quality framing takeoff and the tricks you can use to help save money in the long run, you can improve your company's profitability without adding an expensive estimator to your company's liabilities. Instead, why not check out 1build's cost estimating services? Rather than hiring an estimator for your company, simply use one of our expert estimators to produce a budget when you need us. Why not send us plans for your next project? There's no cost until you actually decide to use our services, and we're happy to help you win big jobs, like our recent win for Hunt & Collins' $3.7 million bid.
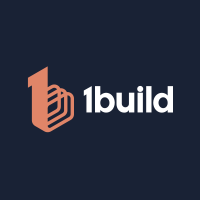
1build provides an easy-to-use integration with construction supplier catalogs and purchasing systems. Get access to millions of construction materials with our API today