The New Paradigm: Why Eliminating Construction Waste Is Essential for Profitability in a Post-COVID-19 World
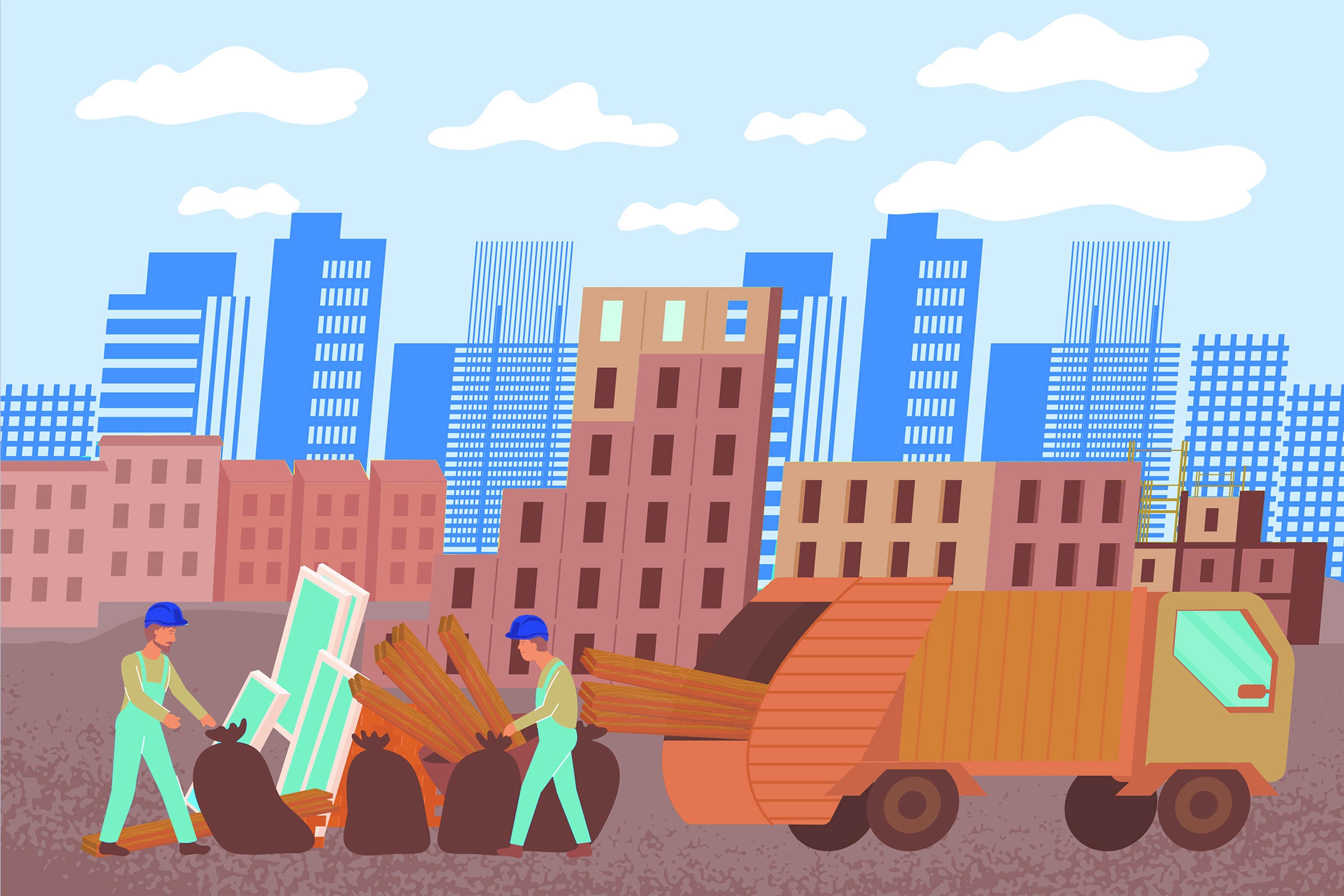
6 Ways to Eliminate Construction Waste to Improve Profitability
Prior to 2020, many construction companies had already begun to shift to leaner operations and digital transformation. But with COVID-19 negatively impacting the construction industry for at least 18 more months, this shift is being accelerated.
Waste in the construction industry takes many forms. Material construction waste in the industry is estimated to reach almost 2.2 billion tons every year by 2025, adding to the environmental concerns faced daily by many around our world. But beyond simple material waste, wasted time and effort must also be reduced or eliminated for construction companies to continue growing in today's competitive marketplace.
Industry studies have shown that half or more of the effort required to complete a construction project is non-value-added, creating exceptional opportunities to improve efficiency. As the construction industry continues to roll through digital transformation and adopt lean and agile principles to improve efficiency, eliminating construction waste will become essential for construction businesses looking to remain profitable in a post-COVID-19 world.
1. Use smarter estimating software to eliminate wasted construction material
Of all the areas of construction waste, overproduction is the most problematic. When you're estimating a project, does your estimating software automatically create cut lists for you to avoid construction waste? For a low back wall reaching six feet tall, is your software estimating two eight-foot studs or one twelve-foot stud to be cut onsite? Is it using the same outlet boxes in almost every situation so waste from a bulk buy for one project can become materials for the next? There are many ways that the right construction estimating software can help reduce your excess materials, which in turn leads to less overall waste on the project.
2. Task specialization to improve onsite efficiency
Focus on developing high-performance teams, which break down traditional silos, assess strengths, and optimize performance. When you have employees who are particularly good at specific tasks, keep them working on those tasks to maximize efficiency. If Carl has a knack for pulling cable and Julie is the fastest on your crew for installing outlets, why would you have both of those individuals doing both jobs? Pay attention to which members of your crew do tasks more quickly and assign them to those tasks to help improve your overall time efficiency. Bear in mind that doing a task quickly and doing it well have to both apply; if getting the task done quickly means damaging materials, this doesn't really save you any wasted time or material. Likewise, reward efficient crews and workers to increase efficiency and eliminate waste.
3. Reduce overhead expenses at the office
Does your business structure have a lot of unused space that could be better utilized to rent out, store materials you got a great deal on, or manufacture common assemblies? Does accounting seem to take forever to complete tasks due to a bottleneck or poor performance? Are you with the same insurance company for the past ten years and have never checked competing rates? If you can answer yes to any of these questions, it's time to take a solid look at how you could reduce your business's overhead expenses to minimize wasted funding spent in building maintenance, labor, or expenses. See our top guide on how to improve construction profitability.

4. Outsource administrative tasks; Reduce downtime
Two-thirds of construction businesses report that more than 25% of work hours are spent waiting for work to be done and 75% of businesses spend less than half their time doing actual construction work. Does your business really need an in-house accounting, marketing, or IT team? Probably not. By outsourcing these tasks, you're going to save money overall through reduced rent, employee benefits, and similar expenses. Are your workers sitting idle due to change orders or lack of equipment? What about sending your workers to pick up and deliver materials to the job site while paying union wages? Outsource your material delivery to an outside company that does exactly that so that you can keep your employees doing what they do best: building houses and structures for your clients.
5. Bid on projects within your expertise
It can be really tempting to bid on a big commercial job to help keep your company going, but if you don't have experience with projects of that type of scale, you may be getting in over your head. Even if you win the bid due to competitive pricing, you may not be able to keep up with the project’s pace, have the right contacts for bulk pricing on materials, or a crew that can adapt to significantly different systems than they are used to. These situations are a recipe for construction waste, whether it's materials, lost time spent figuring out new skills, or excessive overtime to catch up with the pace of the project. Reduce this waste by bidding only on jobs within your expertise. Learn more about best bidding best practices in our #1-ranked guide.
6. Find upcycling and recycling opportunities to reduce construction jobsite waste
It’s estimated that construction waste results in 3 billion square yards of landfill each year. When you can't avoid waste on the job site, try to find opportunities to reduce the amount of waste going into the landfill. Upcycling organizations such as Habitat for Humanity will often take old doors, windows, countertops, cabinets, sinks, light fixtures, leftover project material, and similar waste that would otherwise end up in a dumpster while providing you with a tax write-off. Scrap metal recyclers will take a range of metals from your job site while giving you cash for the material, decreasing your expenses. Many individuals and businesses will come to your job site to salvage materials that you would otherwise trash.
By taking these aspects of the construction process into account, you can quickly reduce material, effort, and cost waste on your job site, making it easier to turn a tidy profit and find new referral projects in the future. Adding these processes before or even during digital transformation can also help make these principles a part of your company culture. Reducing waste will not only become easier as your company becomes a lean and agile entity through digital transformation, but will also serve to insulate your firm from new market constraints brought on by the pandemic. One of the best ways to reduce construction waste and improve your firm’s profitability is to leverage a cost estimating service. Rather than hiring an estimator for your company, simply upload your plans when you have a project, using a dynamic combination of AI and human experience to come up with an accurate takeoff of your project. Sign up today to learn more and see 1build in action.
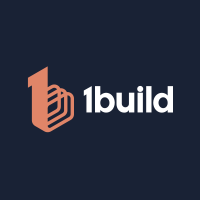
1build provides an easy-to-use integration with construction supplier catalogs and purchasing systems. Get access to millions of construction materials with our API today